Wire parts and metal strips
Wire parts
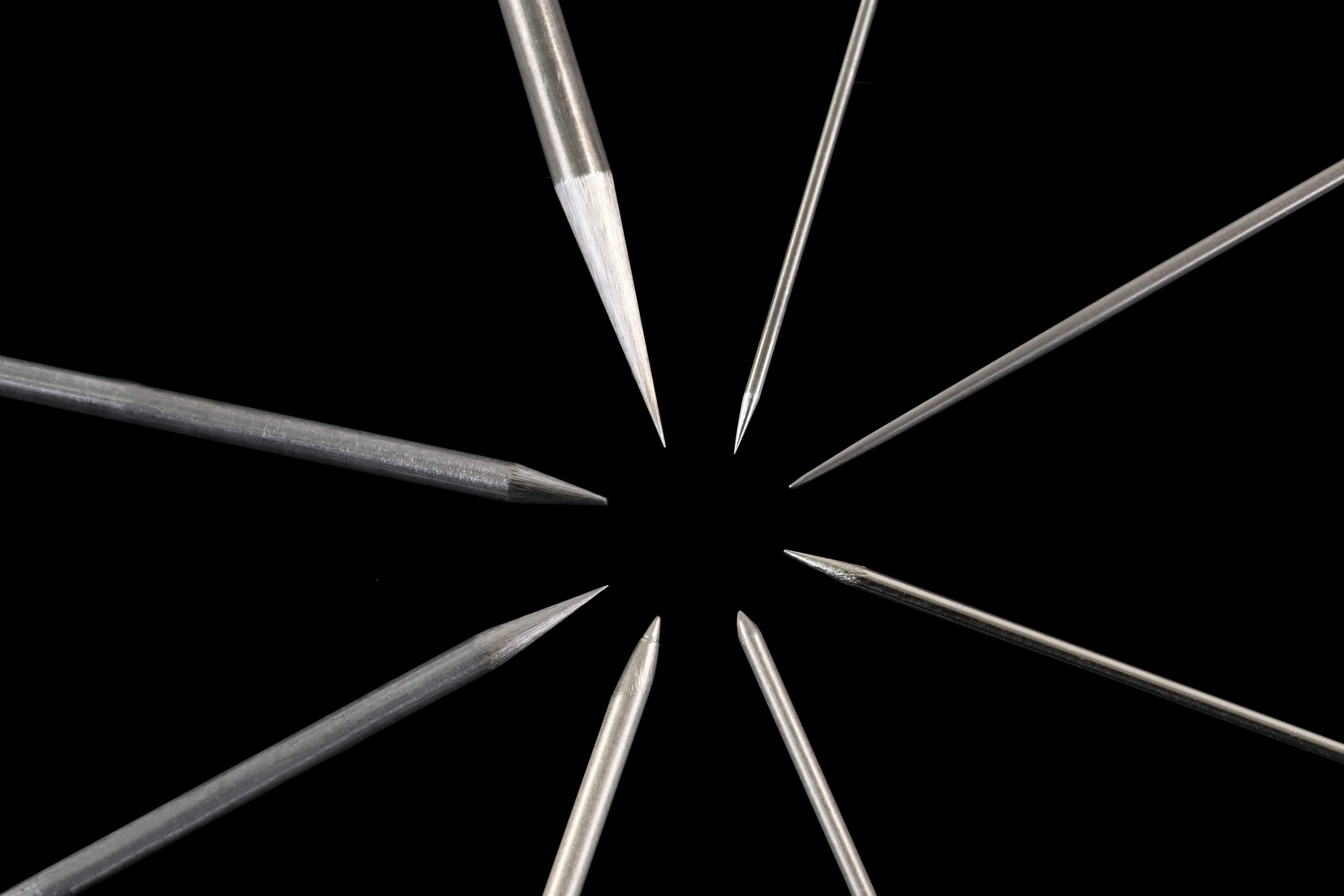
Drawing on its long experience in manufacturing needles, Axfil is constantly developing its knowledge and expertise to precision-make tips, chamfers and rounded ends using metal wire, to meet even your most demanding requirements.
Our expert precision cutting and straightening processes produce metal wire that is perfectly straight, an essential preliminary stage to manufacturing curved, stamped or pointed parts with precision and repeatability.
Metal wire straightening
Straightening, an essential first stage for high-quality wire working, is a long-standing expertise of Axfil due its experience manufacturing needles.
The process involves releasing the wire’s internal residual constraints and removing the bends caused from being wound around a reel during storage, and to make it perfectly straight while retaining all of the material’s mechanical properties in terms of resistance, elasticity and ductility.
Our operators have all the necessary technical expertise to perform this delicate operation, and work on the machines and processes daily to continue improving their techniques.
Metal wire cutting
Cutting is a fine art in which Axfil technicians excel, adjusting all of the settings for a perfect cut, whatever the material or thickness of the wire or strip, with no tearing or burring, and no deformation or marking of the wire surface.
Careful handling of the cut surface is key to ensuring dimensional precision for tolerances up to ±0.02 mm.
Rounding of end sections
Rounding involves creating a half-sphere at the end of the part. This can be done by traditional grinding (manual or automatic) or by local melting using a high-power laser for wires of Ø 0.20 mm to Ø 0.90 mm.
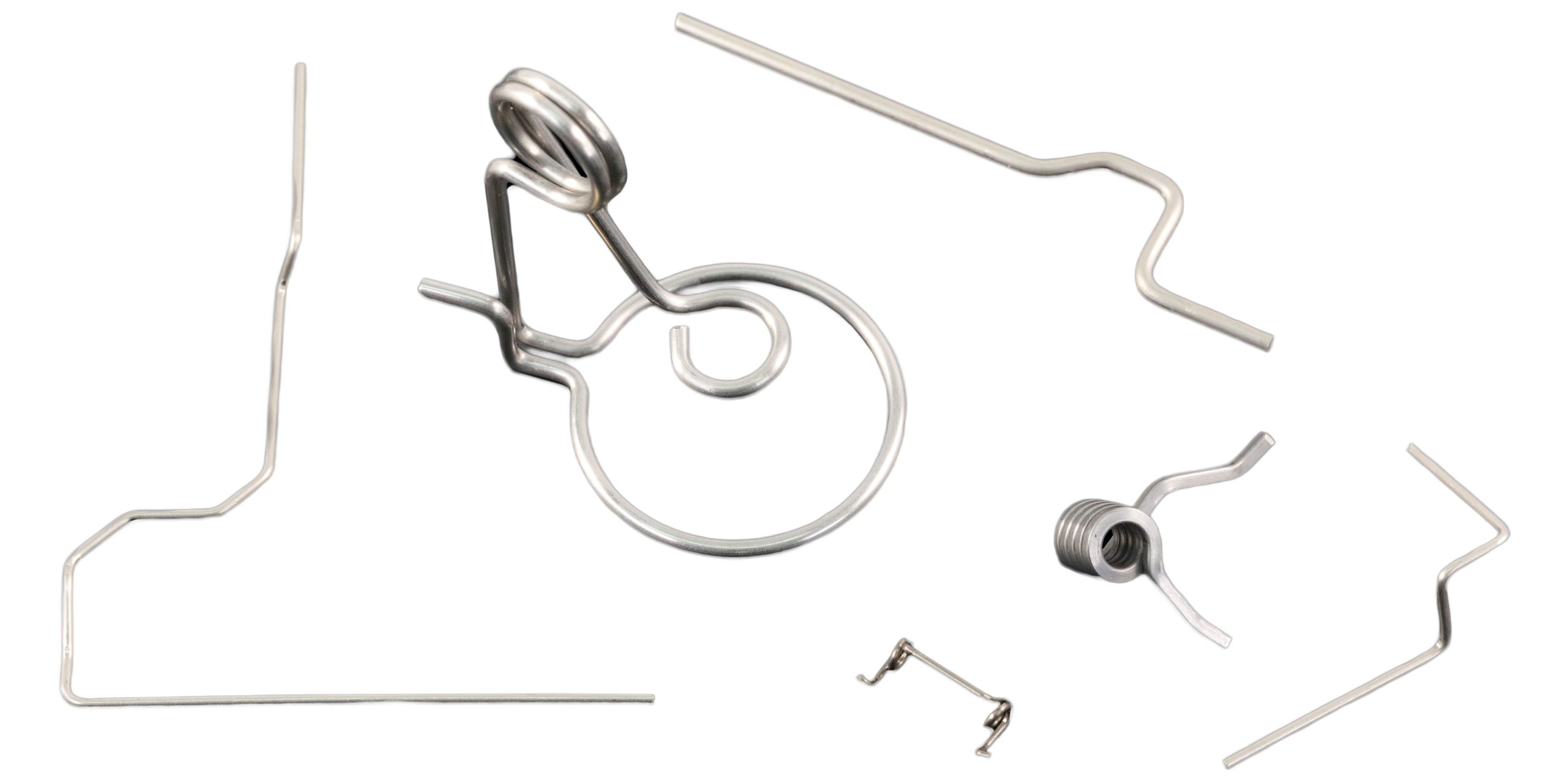
Wire stamping
Stamping consists in deforming a wire part or strip by flattening it out and forming it into a specific shape. This process, perfectly repeatable if the tools are well designed, delivers high performance at a competitive cost for parts produced in large-sized batches.
Stamping also reinforces the mechanical fatigue strength of components by maintaining the material’s grain flow, and increasing its hardness by strain hardening, in comparison with machining or casting. It can then be heat treated to strengthen or stabilise its mechanical characteristics.
Our engineering and design team can advise you on the many technical options available with this manufacturing process and can assess the feasibility of your project based on the particular material and form you want. Stamping can then be followed by a thermal or surface treatment in line with the customer’s needs.
Cold heading
Cold heading consists in deforming the end section of a wire in the direction of its axis to give it a specific technical form. The most traditional application is to make the head of an industrial rivet. This technique can be adapted to create a shape in the centre of a shaft or shoulder type part. This process delivers high performance at a competitive cost for parts produced in large-sized batches.
Axfil’s expertise lies in its knowledge of materials, tool design and impact settings, precisely controlling the deformation process and ensuring repeatability and consistent quality in the end result.
Pointing and Chamfering
Pointing and chamfering involve working the end section of a part using a profile wheel and abrasive elements to create a tip which can be as fine as several 100th of a millimetre.
Axfil’s technical experts will define the process routing and type of abrasive needed depending on the required profile, fineness and surface condition of the tip.
- Based on a wire with a 0.20 mm to 6 mm diameter
- Angle precision: ±0.5°
- Profile of tip: conical, ogival, buffed or other (according to your specifications)
- End of tip: fineness of tip in line with specifications, up to 0.03 mm in diameter
- Polishing of tip: machining of final surface in line with your needs
- Tip on square or polygonal wire
Bending
Bending is a key technique in wire working. Our production machines are designed in-house so that they can perform bending operations, including in complex three dimensions, at high capacity.
Creativity is boundless when it comes to designing complex forms and working to extreme levels of precision, of around 100th of a millimetre. Our standard applications are reinforcements for overmoulded plastic parts for cars and interior fittings, power strips for battery connectors and power systems, ophthalmic, cardiac and dental surgical equipment, and various types of springs, etc.
Our technical team can also help you push the boundaries of your creativity and custom-bend your parts and springs in a multitude of ways.
- Diameter: 0.20 mm to 4 mm
- Three-dimensional folding
- Angle precision: ±30’
- Rolling: > 360°
Knurling and rolling
Knurling is a common technique for making metal reinforcements used in plastic injection overmoulding processes. The indentations caused by knurling increase the resistance of the mechanical bond between the plastic and its reinforcement and protect against the stresses of tension and torsion.
Rolling is a cheaper alternative to machining and can be used to make grooves on the cylindrical part by deforming the material. In addition to its lower manufacturing cost, reinforcing mechanical resistance by strain hardening the area worked offers a major advantage over traditional machining for parts under heavy stress. However, the procedure does require small radii in the groove base and at least one surface with a slight clearance angle.
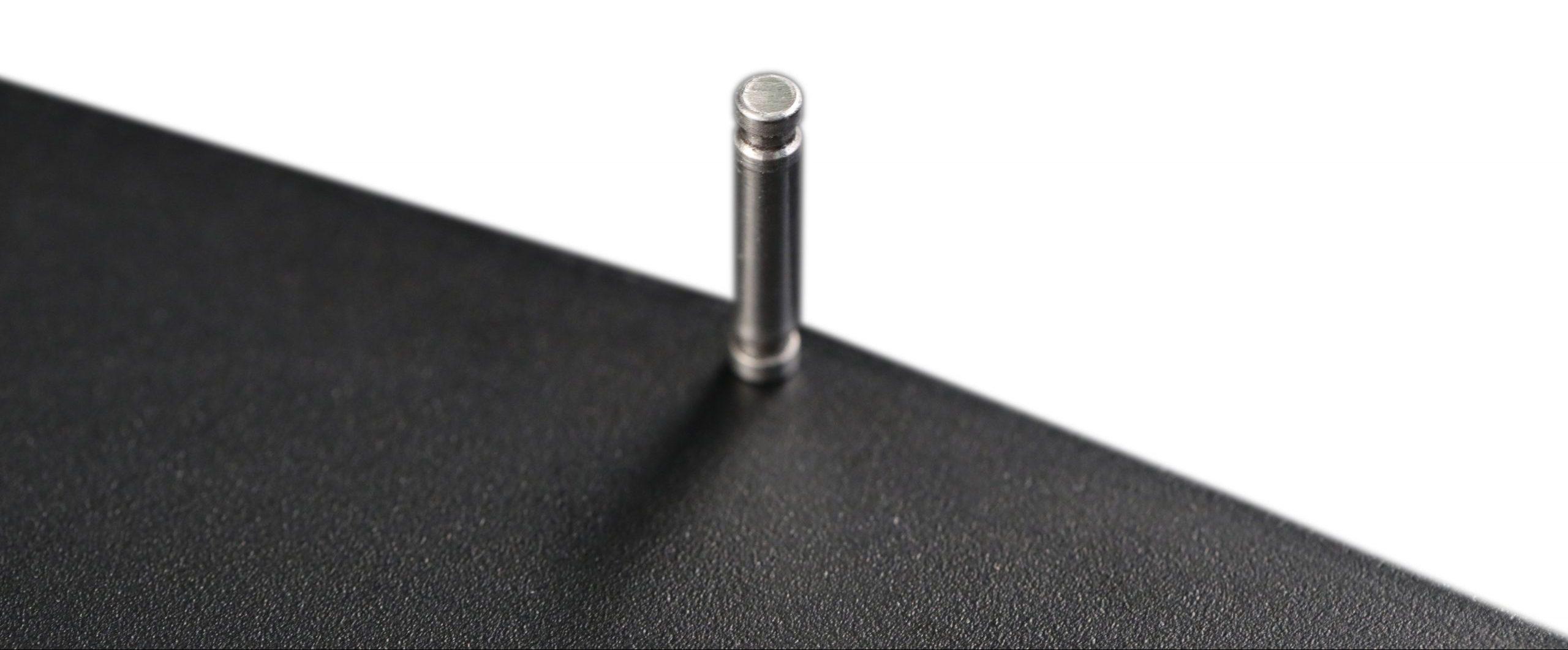
Turning
Along with our expertise in metal wire working, we also offer traditional machining using a turning lathe for working on end sections, including those with long profiles, while maintaining perfect straightness: grooves, indentations, piercing, threading, etc.
Precision polishing
Axfil has all the tribofinishing resources needed to deliver the most demanding levels of roughness (Ra, Rz, Rt, Rmr, etc.) by adjusting the polishing settings with precision and stability. Drawing on its experience in this field, our technical team can identify the most suitable polishing methods and routes in line with your needs, together with inspection routes to ensure the stability of the end product.